REMOTELY OPERATED WATER VESSEL FOR EMERGENCY RELIEF (ROWVER)
Context:
My yearlong Senior Capstone Project consisted of 3 members including myself. After being matched with a client who gave us our project prompt, the team worked at project development and modeling while remaining within the constraints of the project ($200 budget and a semester for proof of concept/a semester for design). This project was then presented at the Senior Engineering Seminar to be approved by our client based on completion and feasibility.
​
Background & Problem Statement:
- There is an average of 48 hurricanes per year worldwide
- Specifically, in 2020, flood claimed the lives of 6,000 people and affected 34 million others.
​
With this, People need a more reliable way of survival following a natural disaster such as flooding without endangering a rescuer.

Project Approach:
After meeting with our client, many guidelines were defined for what the ROWVER must do

Concept Development:
A Pugh Analysis (also known as a decision matric method) was performed that ranked out concepts based on its ability to best meet our set of criteria. Knowing that our most important requirements were speed and safety for both the rescuers and the victims, we saw it best to create a remote-controlled vessel that has two separate stages of deployment.

The ROWVER works as follows:
1. A user deploys the ROWVER module from their location. Once deployed, it may be remote controlled to the location of the victim using the camera attached to the deck of the module.
2. Once the victim is reached, a pneumatic system is activated that creates an inflation region that surrounds the ROWVER module, allowing the victim to board the new 2nd stage of the ROWVER.
3. Equipped with a audio system that allows for two-way communication between the user and the victim, along with an installed storage kit that provides safety kit components if necessary, the victim is guided back to safety.
4. The inflated region may be deflated as necessary, and the process is then repeated.
​
The two stages, prior and after inflation, were decided based on its ability to meet the necessities of the device. To ensure speed to the victim, we saw it best to not have the inflated region, as it first applies unnecessary drag to the ROWVER and also makes it more difficult to maneuver. Once they reach the victim, the region is activated to prioritize the safety of user as they are taken back to refuge.
​
Design Decision & Feasibility:
Due to the complexity of the ROWVER, it was divided into 3 separate subsystems shown below. I was tasked with the module of the ROWVER.
​
To maintain this report as a brief summary of the project, slides have been made to encapsulate each subsystem.
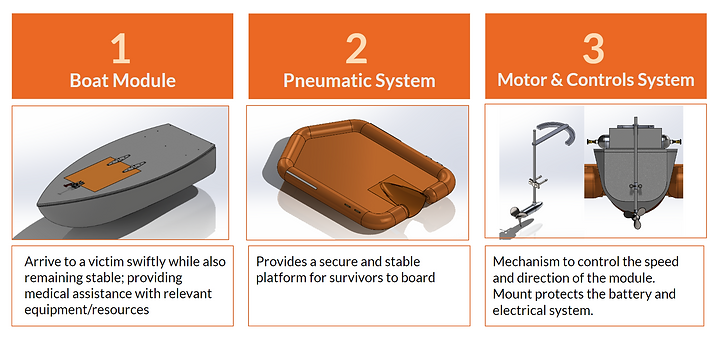
Module:
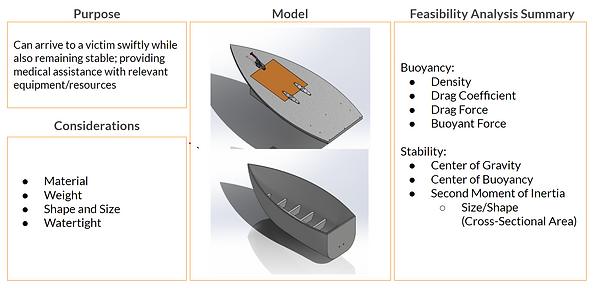
The module on its own must be able to not only maintain its own weight and float, but to remain stable as it maneuvers through floodwater. Because of this, several considerations were made as described above. When designing this in SolidWorks, there was sufficient information given by the software that allowed me to make Buoyancy calculations. By calculating that the buoyant force was greater than the force of gravity and the thrust force from the engine was greater than the drag force, proof could be made that the model is considered to be buoyant. Stability was calculated using several relevant characteristics such as the center of gravity and center of buoyancy. SolidWorks allowed me to see that the center of buoyancy is above the center of gravity, proving stable conditions. Using the calculated Second Moment of Inertia and comparing it to the center values, it can be assumed that the model is stable if it were to be manufactured.
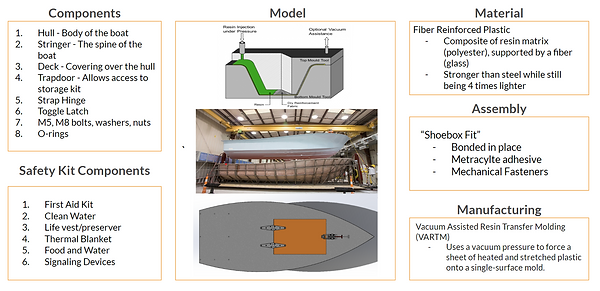
Given many other complexities, such as the additional storage kit (denoted in orange in the model), the need for the hull and the deck to be assembled, and ensuring the body is watertight, a component list was made that includes all of the most important parts. Several materials were considered, but Fiber Reinforced Plastic was chosen due to its feasibility compared to other materials such as Carbon Fiber Reinforced Plastic and Aluminum, as they are much more expensive and difficult to acquire. The assembly of the hull and the deck is that of a shoebox fit, bonding both pieces together to mitigate any areas of leakage. Finally, the major body parts of the module will be manufactured using vacuum assisted resin transfer molding, a very common process used to make FRP boats.
​
Pneumatic System:


Motor & Controls:

Final Model:

Conclusion:
There are few loose ends of this Senior Capstone Project that we were not able to accomplish. First and most importantly, a prototype could not be made due to the time and budget constraints. Along with that, there i not sufficient information on the controls aspect of the project, which aims to make the ROWVER remotely operated. Although we do have these parts of the project incomplete, I do believe that my team has left this project in a good state for a future Senior Capstone team to complete.